DAF in Action
‘No emission-free transport without the right infrastructure’
Politicians have to make a move, it’s time for action. That is the message being sent to Europe’s politicians by Patrick Dean, DAF’s Chief Engineer Vehicle Development. Let there be no mistake, says Dean: without the right network of charging and filling stations for hydrogen, carbon-neutral transport is simply not possible.
By: Henk de Lange
Your message is crystal clear...
“It is. And it has to be. All truck manufacturers, including DAF, are working extremely hard to find clean and sustainable transport solutions. Whether it concerns electric trucks, hydrogen-powered trucks, hybrid vehicles or ultra-clean diesel trucks using synthetic (clean) fuels, DAF already has the required technology or is testing it. And we also know that both transporters and their customers want zero-emission trucks. However, if our XD Electric can’t be charged after it has left the factory because there are not enough charging stations, what then? It’s time for politicians to start making sure that the infrastructure for zero-emission trucks is in place. And as soon as possible, too.”
What do the politicans need to do?
“Europe has set the truck industry challenging and demanding goals. All the trucks rolling off our assembly lines in 2025 time must emit 15% less CO2 than the vehicles we manufactured in 2019. And, according to the latest information, this will have to be 45% by 2030. Reaching these targets by optimising existing technologies alone is just not possible. We have to explore new avenues if we want to get serious numbers of emission-free trucks out on the road, in addition to the efficient diesel trucks that we are currently building.
More and more European cities are now refusing to allow trucks with a diesel engine into their city centres. So our customers have to switch to using electric or hydrogenpowered trucks. But if they can't recharge or refill along the way, the shelves in the shops will soon be empty. So it’s up to the politicians – who are the ones demanding emission-free trucks in our cities in the first place – to ensure that those trucks can actually drive. They have to enable and encourage investment in the required infrastructure.”
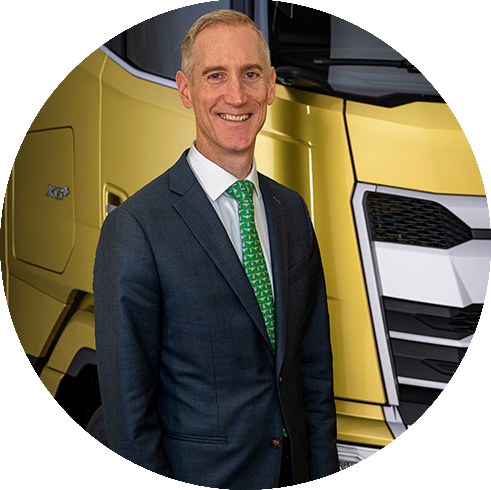
“It’s time for politicians to start making sure that the infrastructure for zero-emission trucks is in place. And as soon as possible, too”
Patrick Dean,
DAF Chief Engineer Vehicle Development
Where does DAF stand?
“We are the frontrunners in the development of zero-emission trucks. With our XB, XD and XF we already have a complete series of electric trucks with a range of up to 500 kilometres and we have also completed very successful field tests with hybrid vehicles. The development of the zero-emission hydrogen combustion engine is very promising and in the US our parent company, PACCAR, has carried out a successful long-term test together with Shell and Toyota on trucks powered by fuel cells. That test resulted in an even more intensive partnership with the aim of developing emission-free versions of the Kenworth T680 and Peterbilt 579 equipped with Toyota’s fuel cell technology and launching them on the market. We are following these developments very closely, of course.”
A hydrogen combustion engine? And fuel cells?
“There are two options for using hydrogen in a truck: by means of a fuel cell or hydrogen in a combustion engine. In other words: you can inject hydrogen into an engine but you can also have it react with oxygen in a fuel cell. The chemical reaction produces electricity that can be used to power the electric motor in a vehicle. In the case of each driveline the result is the same: all that comes out of the exhaust is water vapour. One of the big advantages of hydrogen is that you can refill very quickly. In a few minutes you’re ready to drive another five hundred kilometres.”
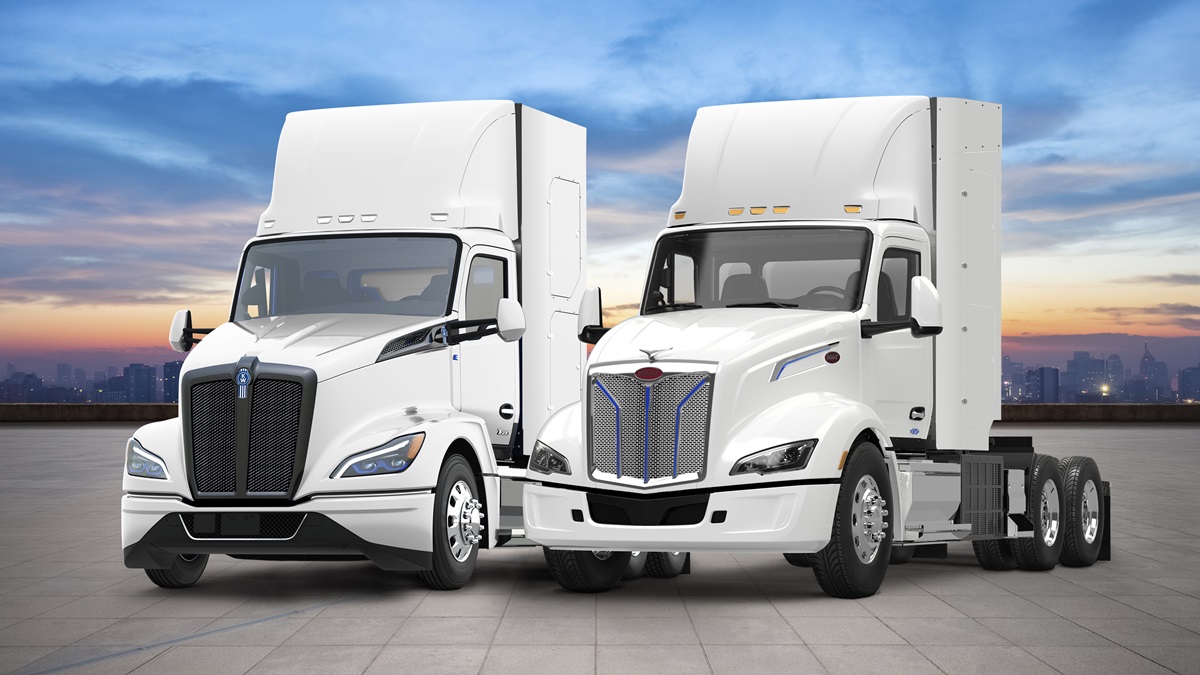
Emission-free versions of the Kenworth T680 and Peterbilt 579 equipped with Toyota’s fuel cell technology will be developed and launched on the market.
The ideal solution!
“Yes, but it’s not as easy as it sounds. Because hydrogen needs electricity to produce it. The fuel cell is technically quite complex and expensive and it takes up a lot of space in the chassis, but the hydrogen combustion engine is a very promising and sustainable alternative – better understood technically speaking, less sensitive to the quality of the hydrogen, about the same size as a diesel engine and based on existing technology that we have here in Europe.”
What about electric trucks?
“We can cover around 500 kilometres today with an electric truck and that’s not sufficient for international transport. Charging an electric vehicle also takes more time and there aren’t enough charging stations, either. However, at the moment, electric trucks are the most logical zero-emission solution for regional and urban transport. Another option is the use of diesel-electric hybrids and, eventually, hydrogen vehicles on the motorway that can switch over automatically to electric power in the city.”
Do all roads lead to Rome?
“They do! There won’t be a one-size-fits-all solution for all transport applications but DAF will continue to explore several different paths. We need the support of governments to roll out a filling and charging station infrastructure managed by third parties. These are challenging times but we will get there if we pull together and work hard.”
DAF Electric Truck Assembly is state-of-the-art
DAF remains at the forefront of the development of sustainable trucks. With its XB, XD and XF Electric, the Dutch truck manufacturer already has a complete series of zero-emission vehicles with a range of up to 500 kilometres. Most of these trucks will soon be rolling off the assembly line at the company’s brand new factory for battery-electric trucks.
By: Henk de Lange
The new DAF Electric Truck Assembly is located at DAF’s largest production facility in the city of Eindhoven (NL) and covers an area of 5,000 m2. The factory has two sub-assembly lines: one for the preparation of battery packs and one for building the Electric Drive Module. This module consists of a front battery pack, a relay box for connecting the high-voltage systems and the electric auxiliary systems. These primary components are mounted on the chassis on the main assembly line – which measures almost 150 metres in length – along with the e-motor and integrated gearbox.
New generation of battery-electric trucks
DAF has opened its Electric Truck Assembly plant for the production of its latest generation of battery-electric trucks. The DAF XD and XF Electric are available in a variety of axle configurations. They are powered by PACCAR e-Engines and equipped with 2 to 5 battery packs (210 to 525 kWh), enabling a range of up to 500 kilometres. Thanks to their modular design, the trucks can be tailored to match the needs of the customer. With careful planning of routes and battery-charging, it is possible to cover 1,000 zero-emission kilometres per day. The battery packs can be charged up to 80% in only 45 minutes when using rapid charging (up to 350 kW). DAF expects production to number in the thousands each year in the near future, which is in line with the rising demand for fully electric trucks.
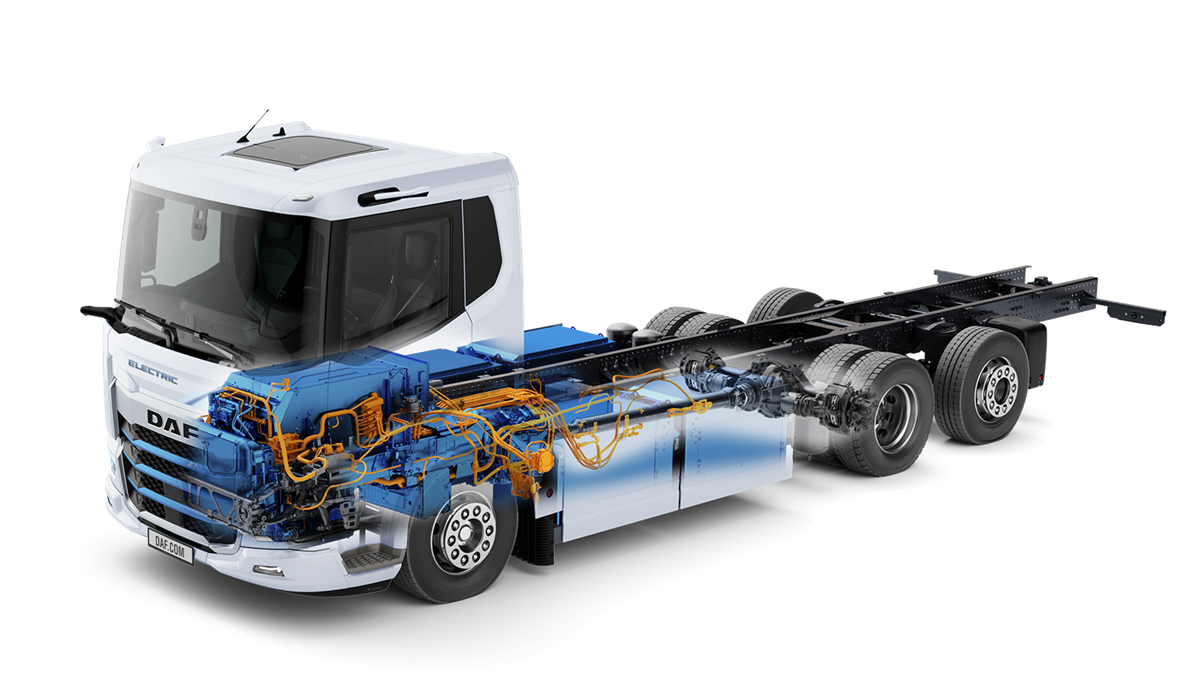
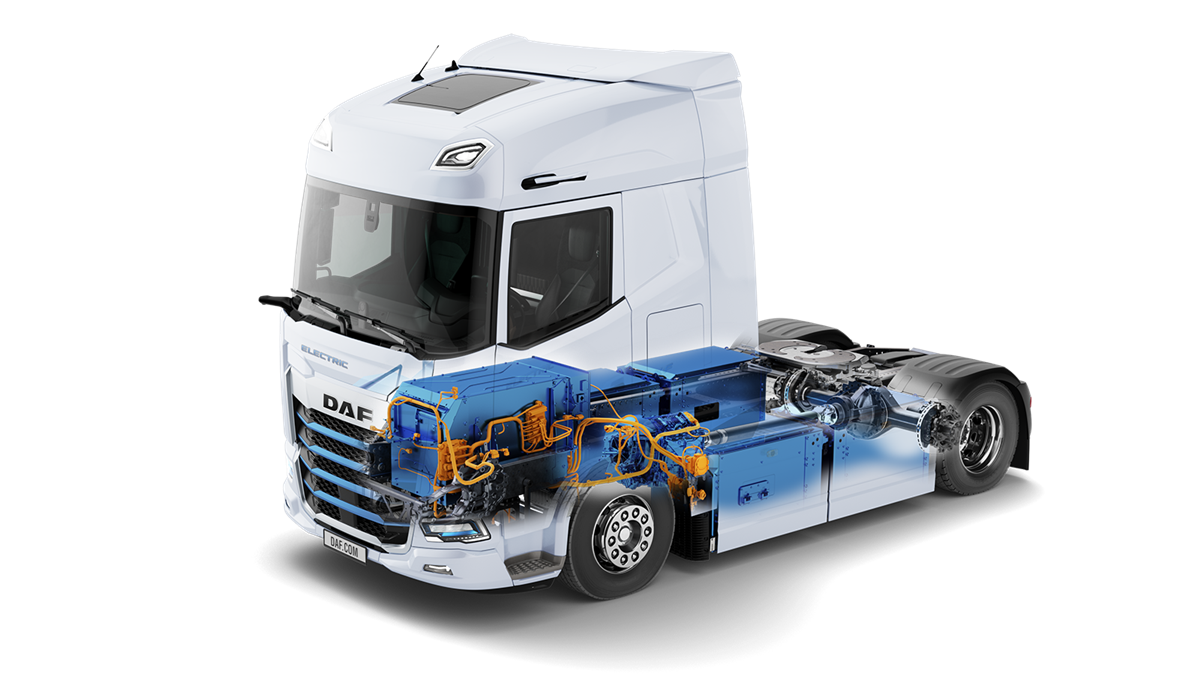
The DAF XD and XF Electric are available in a variety of axle configurations. They are powered by PACCAR e-Engines and equipped with 2 to 5 battery packs (210 to 525 kWh), enabling a range of up to 500 kilometres.
Minister: “DAF leading the way”
DAF’s new Electric Truck Assembly was officially opened by the Dutch minister for Economic Affairs and Climate, Micky Adriaansens. “DAF has been a leading player in the production of trucks for many years,” she said. “And DAF is now also leading the way in innovations in electric transport. The transition towards cleaner production and products is very important. Not only for the environment but also to ensure that the Netherlands remains competitive. This new factory for battery-electric trucks is a shining example of this ambition.”
Important step
“The opening of the DAF Electric Truck Assembly plant represents a new and important step on the road to a cleaner future,” according to Harald Seidel, president of DAF Trucks. “In our efforts to support our customers in the transition towards zero-emission road transport, we go much further than just providing them with first-class, fully electric trucks. Our complete package comprises a wide range of charging stations, tailor-made advice on the planning of routes and battery-charging and training programmes that help drivers get the most out of their electric vehicle.”
PACCAR Parts – celebrating 50 years and looking to the future
When describing PACCAR Parts, the components division of DAF Trucks’ parent company, one number stands out: 99. Not only does PACCAR Parts have 99 specialised stores for the sale of universal parts (TRP shops) in Europe, but its score for delivery reliability is also a neat row of nines: 99.99 per cent. Closer to 100% is simply not possible. It is the cherry on PACCAR Parts’ 50th birthday cake.
By: Peter van der Vegt
Established in 1973, this year marks PACCAR Parts’ fiftieth year in business. A milestone well worth celebrating, particularly given the fact that over the past half century the division has grown to become a reputable supplier of over 180,000 parts for trucks and trailers. And that number is steadily increasing, partly due to the current energy transition in the world of transport. Today PACCAR Parts offers a comprehensive range of ultramodern chargers for electrically powered vehicles. “The success of our division is all down to the commitment and efforts of our employees and dealers, who provide our customers with magnificent support every single day,” says Laura Bloch, general manager of PACCAR Parts and also vice-president of PACCAR.
Reliability
180,000 parts. Just think about that for a minute, a number that the founders of the first Parts Distribution Center (PDC) could never have even dreamed of when they opened the doors of the first branch in 1973. That branch still operates to this day in Renton, a city in the state of Washington in the US. The number of PDCs soon began to grow, first in the US and then in Europe before spreading around the globe. Today PACCAR Parts has eighteen PDCs on four different continents covering a total area of 315,000 m2 or forty football fields. PACCAR has four distribution centres in Europe: Eindhoven (NL), Leyland (Lancashire, UK), Budapest (Hungary) and on the outskirts of Madrid in Spain. They supply DAF dealers on the European continent at the highest possible level of reliability: 99.99 per cent, a figure that remains unique to PACCAR in the world of truck parts. It also underlines the importance that DAF and PACCAR place on delivering on time, as everyone in the world of transport knows the cost of an idle truck.
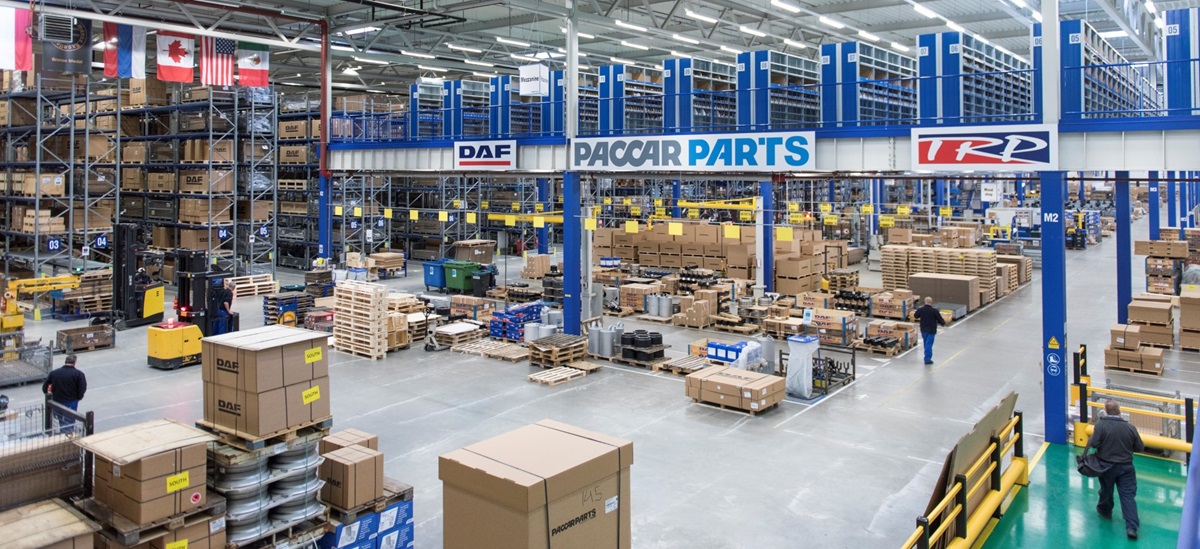
The PDCs supply the DAF dealers on the European continent at the highest possible level of delivery reliability: 99.99 per cent.
2,300 Dealers
Over fifty years the number of dealer locations affiliated to DAF and its sisters companies Kenworth and Peterbilt has grown steadily. In 1973 that number was 180, today it has reached 2,300 worldwide, almost half of which (1,100) are in Europe. Good news for the customer, as the availability of parts has become greater and delivery times shorter.
One stop shop
An important step in the growth of the division was the introduction of the ‘One Stop Shop’ strategy. In 1995 PACCAR Parts launched a chain of shops under the name TRP (Truck & Trailer Parts) to supply transport companies with universal truck and trailer components. With more than 60,000 items, parts and other equipment, the range or products has been expanded enormously and it is seldom that TRP cannot come up with the goods. The TRP network consists of 271 specialised stores in 42 countries around the world, more than one third of which (99 to be exact) are situated in Europe.
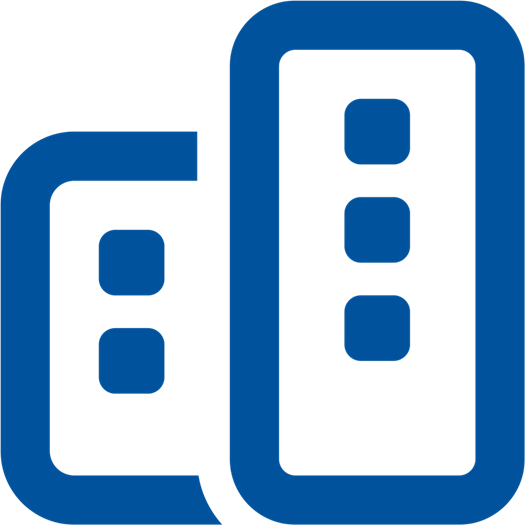
18
Parts Distribution Centers
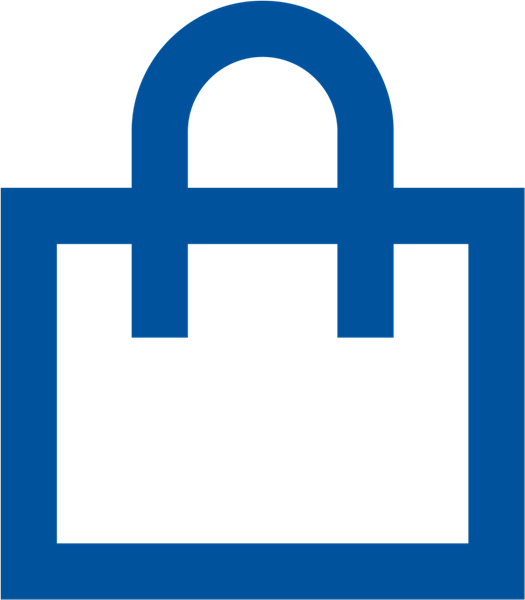
99.99
% delivery reliability
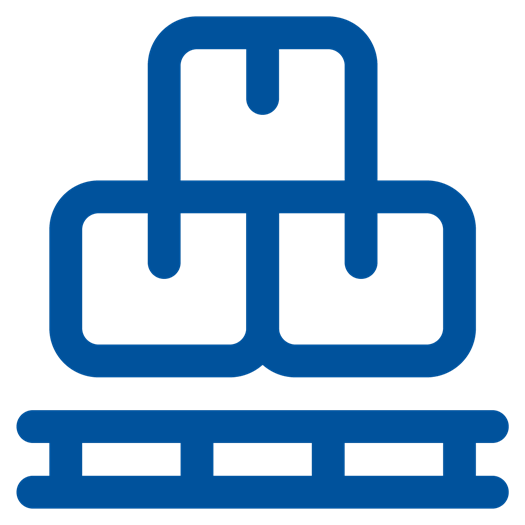
180.000
items in product range
E-commerce
An extensive e-commerce programme was launched to make the division’s services and products more visible. Customers can access the programme 24/7 to find the components they need. PACCAR has also teamed up with other major suppliers to launch a series of innovative programmes aimed at enhancing customer satisfaction. These include PACCAR Parts Fleet Service, which counts over 1,100 fleets in Europe (with a total of 260,000 trucks and 140,000 trailers) among its customers.
PACCAR chargers
“We are more than ready to help our customers with the energy transition,” says Dutchman Dick Leek, general manager of PACCAR Parts Europe, in conclusion. “Through our DAF dealers, we are constantly expanding our range of services and products. PACCAR offers not only a full range of mobile and stationary PACCAR chargers for all types of electric vehicles, but also all the required components.”
Focus on the environment self-evident
DAF takes the environment very seriously in its business operations. It is not without good reason that in 1988 the Dutch company was the first truck manufacturer to be awarded an ISO 14001 environmental certificate.
By: Henk de Lange
DAF strives to limit the impact of its activities on the environment as much as possible. This means constant attention to further reducing emissions and noise and using water and energy as carefully as possible. A full summary of the company’s focus on the environment would run to many pages but we would like to mention a few highlights here.
Cab painting facility
Take, for example, the ultramodern cab painting facility in Westerlo, Belgium that opened in 2017. Thanks to the installation of a highly advanced and partially robotized painting system, emissions of hydrocarbons have been halved. Special nozzles are now much more efficient in their use of paint. The latest cleaning techniques are used to purify the air produced in the spraying booths before it is ventilated and the residual heat is used to heat the pre-treatment and immersion baths.
Water-based paint
DAF started using water-based paints back in 1997 with the aim of reducing the discharge of solvents. Add to this the increased efficiency in the production process and the results are nothing short of spectacular. In 2000 the level of solvent discharge per truck was 20.7 kg, today it is 4.1 kg. A reduction of 80%!
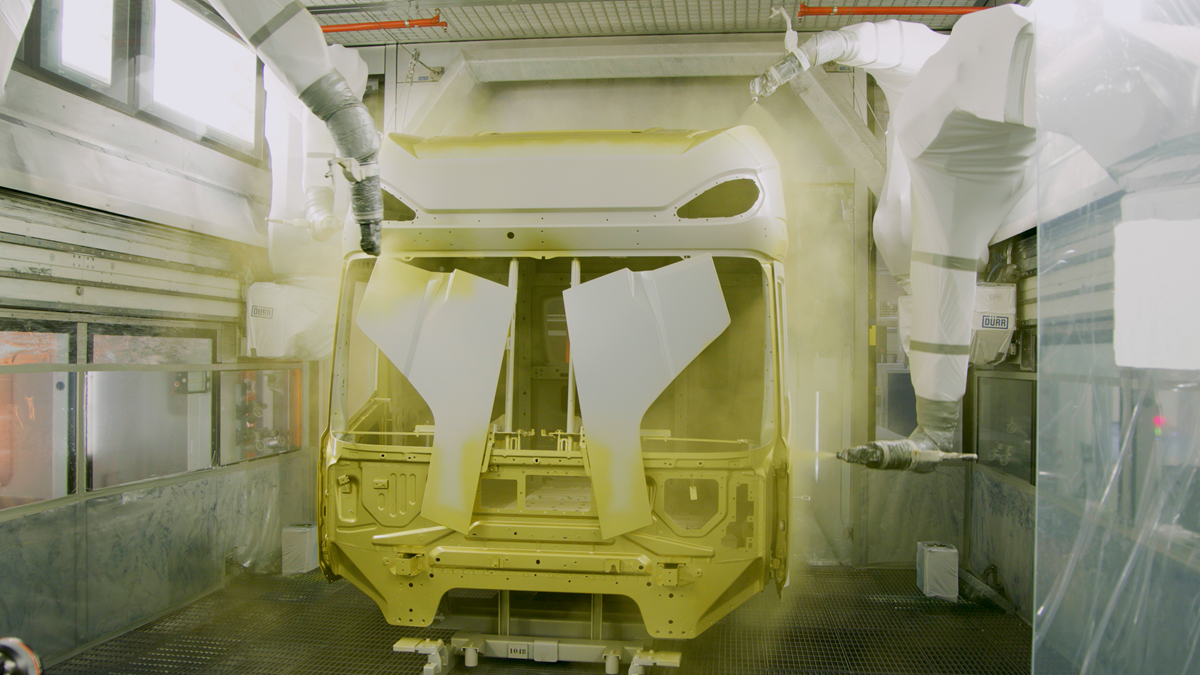
Thanks to the installation of a highly advanced painting system, hydrocarbon emissions have been halved
Water consumption
DAF needs to use a lot of water in its production processes for spraying, cleaning, rinsing and cooling. For more than twenty years, the DAF factory in Eindhoven has been using water from the nearby Eindhoven Canal. The water from the canal is purified two times: first, before being used in the factory and then before it is pumped back into the canal. At DAF’s Axle Factory in Westerlo, every effort is made to use water wisely. The three machines for hardening steel make use of a closed cooling system that significantly reduces water consumption.
Energy and CO2 emissions
DAF has an active programme for saving energy and limiting CO2 emissions. The brakes in the engine test cells, for example, are used to generate electricity. The result is an annual saving of over 10 million kWh. Replacement of the fluorescent lighting in the offices and factories with efficient LED luminaries has led to a saving of 7.5 million kWh.
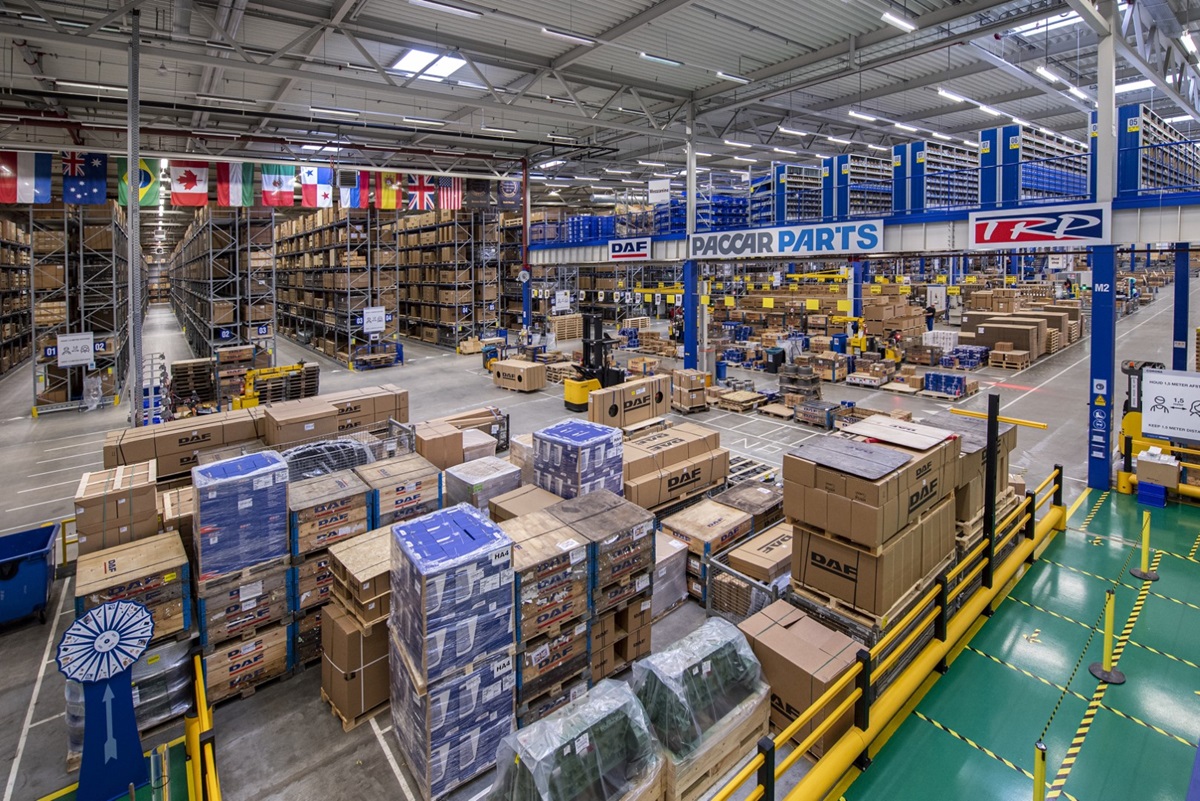
All production facilities have internal targets for reducing the waste that results from packaging and DAF is fully committed to using sustainable instead of single-use packaging
Waste: zero waste to landfill
In 2008 DAF took the decision to stop dumping waste. All waste is now recycled for use as raw materials or for generating energy. For example, steel shot waste is re-used in road construction projects. Even coffee grounds are fermented to produce biogas and the residue is used as soil conditioner or incinerated to generate energy. As a result of these initiatives, Lloyd’s Register has certified DAF as a ‘zero waste to landfill’ company.
Packaging
DAF tackles the problem of used packaging by reusing materials wherever it can in the factory. All production facilities have internal targets for reducing the waste that results from packaging and DAF is fully committed to using sustainable instead of single-use packaging.
Battery Electric Truck Trial in England
The transition from internal combustion engine to electric drive brings a number of challenges with it for haulage operators, drivers and manufacturers alike. The surest way to resolve those challenges is to gain operational experience and the data that comes with it. That has been the aim of the Battery Electric Truck Trial (BETT).
By John Kendall
The project dates back to June 2021, when DAF Trucks was awarded funding from InnovateUK, the UK government-funded national innovation agency, which supports business-led innovation in all sectors, technologies and UK regions. The funding was to cover the deployment of 20 electric trucks operating in public sector fleets across the North-West of England. CENEX, the independent, non-profit low carbon and fuel cell centre for excellence organisation was sub-contracted to provide independent trial monitoring and reporting. The organisation also provided two web-based tools.
No stranger
The DAF LF Electric was the vehicle chosen to take part in the trial. DAF launched the truck in early 2021 and was the first of the major European truck manufacturers at the time to reach the market with an electric vehicle of over six-tonnes Gross Vehicle Weight (GVW). DAF was no stranger to electric vehicles by then, having already launched the CF electric tractor unit. Earlier than that, the LF Hybrid appeared in 2010, combining diesel and electric power, while the production LF Electric underwent several years of planning and trials before the production variant was launched.
Six-year warranty
When the LF electric was launched, it came with a motor generating 250kW of nominal power and 370kW peak. This was matched with a nominal torque output of 1,200Nm (3,700Nm peak), available from zero rpm. The LF Electric was equipped with state-of-the-art batteries using Lithium Ferro Phosphate (LFP) chemistry. In terms of sustainability, LFP batteries do not contain either cobalt or magnesium and the chemistry of the battery ensures the highest thermal safety. The batteries carry a six-year warranty.
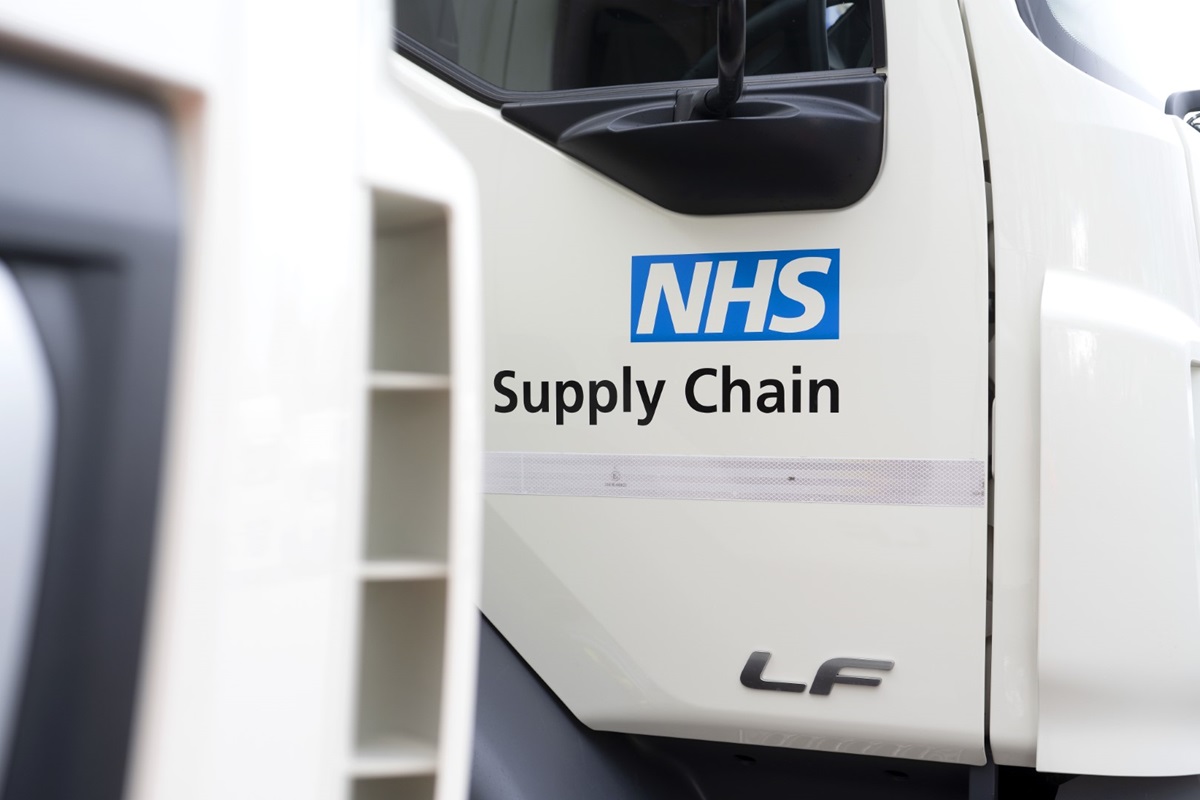
Unipart Logistics is operating eight of the vehicles with temperature controlled bodywork
Twelve hours
The LF Electric benefits from being able to use either slow AC charging or rapid DC charging. Using a 400V 22kW three-phase AC supply, the battery pack can be charged from 20 per cent to 80 per cent in six and a half hours or in 12 hours for a full charge. This works well for back-to-base operations needing only overnight charging. Where charging from a 150kW supply is possible, including some chargers on the public charging network, the batteries can be rapid charged from 20 per cent to 80 per cent in one hour or two hours for a full charge. Depending on conditions and duty cycles, the 282kWh battery pack could carry the LF up to 280km (175 miles). On the LF Electric options list is a 400V e-PTO, which can power auxiliary equipment such as a fridge unit or an electrohydraulic crane. All the vehicles taking part in the BETT were 19-tonne rigids. LF Electric offered several key features that made it attractive to the project. These included a daily zero emission range exceeding 100 miles, the ability to rapid charge the vehicles, no loss of payload by volume and the availability of an e-PTO.
Hospitals
Unipart Logistics is operating eight of the vehicles with temperaturecontrolled bodywork, on multi-drop routes to NHS hospitals around the North-West of England, covering on average around 195km per vehicle per day, delivering roll cages of stock to hospitals. “The main advantage is the reduction in carbon output compared with diesel”, says Paul Ellis, Head of Transport, NHS Supply Chain at Unipart Logistics, “Fuel running costs are lower than diesel, otherwise, the function is the same as all our diesel vehicles.”
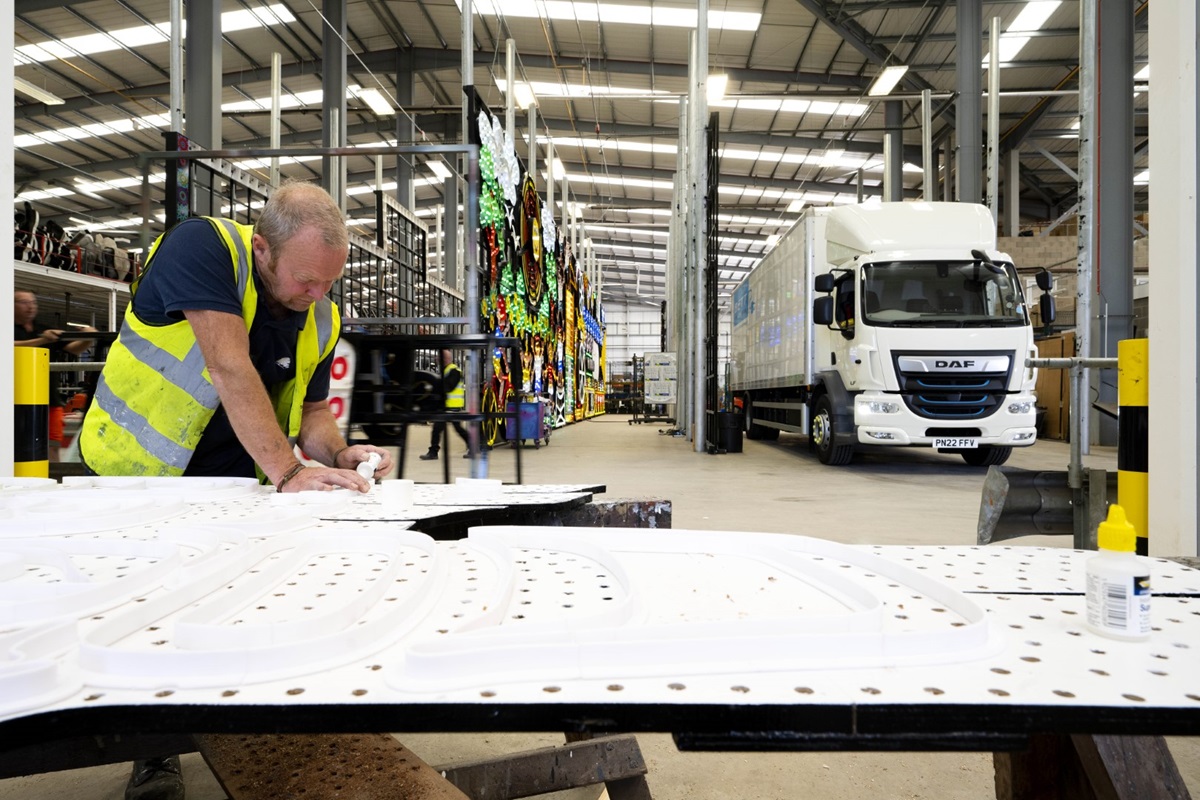
Illuminations
Blackpool Council is operating one of the BETT vehicles and it is involved with a very different kind of work from the NHS Unipart Logistics vehicles. The renowned Blackpool Illuminations were first switched on in 1879 and have been a key part of the town’s autumn and winter visitor attractions ever since. The Illuminations now cover a total length of 10km along the Blackpool promenade. The Blackpool BETT vehicle is involved with local multidrop deliveries and collections for the illuminations, features and associated equipment. Most of the journeys are along the Blackpool promenade, with occasional deliveries and collections to Lancaster, Chorley and Leyland, all within a 75km radius of the seaside holiday town. Thanks to LED lighting technology, the Illuminations now consume around 33 per cent of the electricity needed to light them 10 years ago, an impressive energy reduction. Using an electrically powered truck which costs less to run and generates zero tailpipe emissions is very much in keeping with those energy reductions.
Concern
The greatest concern expressed by all operators before the trial started was about the vehicles’ ability to cover the range needed for daily operations. We asked Paul how this has worked out in practice with the NHS BETT vehicles, “Performance is good, vehicle capacity and operational functions as good as diesel. Range is not as good as expected yet, with a maximum of 150 miles (242km) on a full charge the best achieved so far.” With the NHS Supply Chain vehicles covering some of the higher daily distances in the trial, rapid charging units have been installed on the sites where the vehicles operate. With chargers capable of delivering up to 187kW, the vehicles can be re-charged in less than two hours.
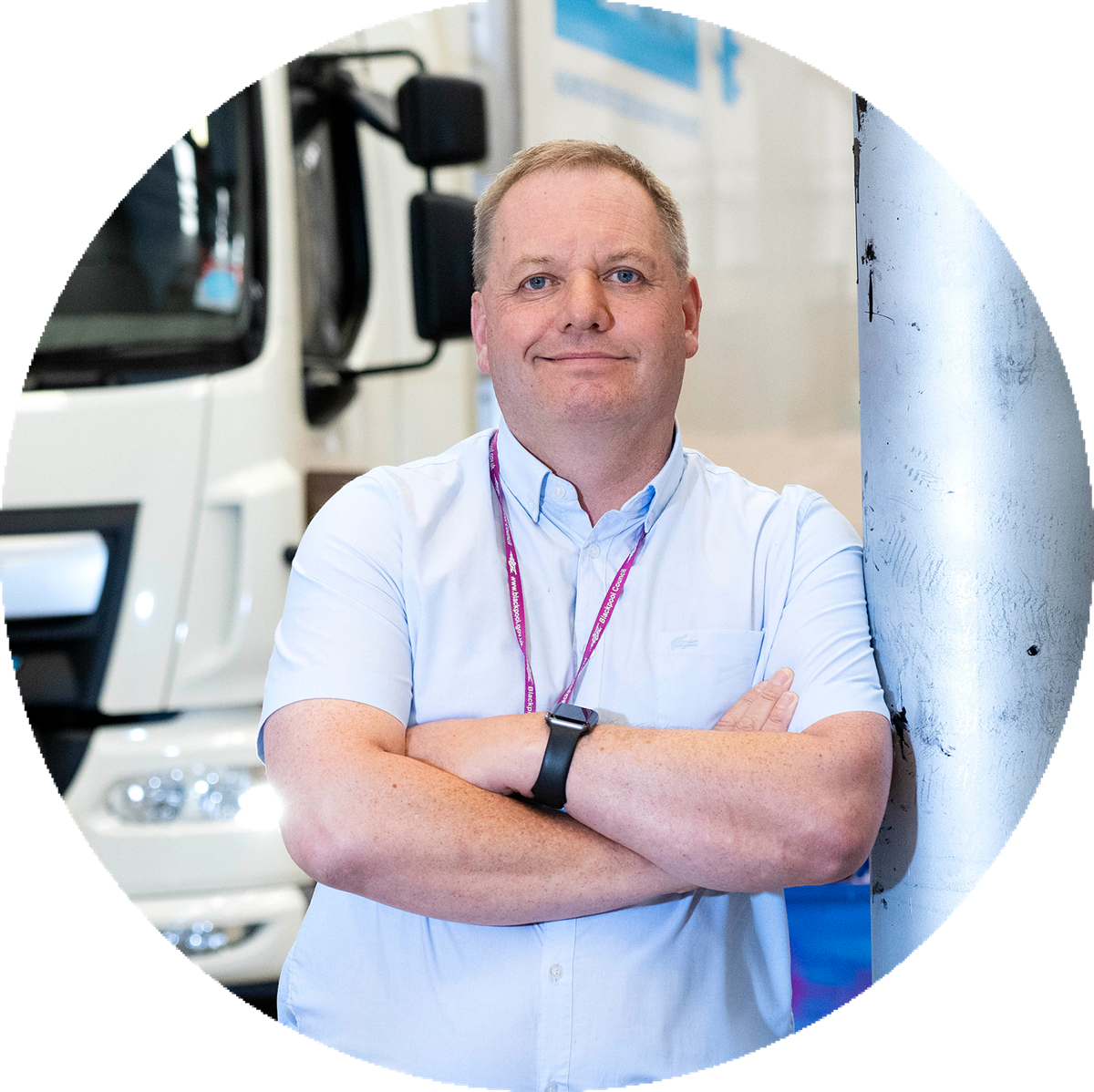
“The driver experience is great. The drawbacks are range, the charge time and available charging infrastructure.”
Richard Williams,
Illuminations Manager at Blackpool Council
Infrastructure
Richard Williams is the Illuminations Manager at Blackpool Council and he has had a similar experience, “The driver experience is great. The drawbacks are range, the charge time and available charging infrastructure.” While truck manufacturers can decide how much battery capacity to build into a vehicle, the charging infrastructure in the UK is currently one of the issues facing all operators of electric vehicles.
Comfortable, fast and quiet
CENEX found that before the trial started, drivers had great expectations of their vehicles where performance and comfort were concerned. Richard reported that feedback from his drivers was positive, “The vehicle runs well and is comfortable, while start off acceleration is better than diesel.” Paul’s drivers appear to be equally happy, “It’s a great driving experience”, he says, “Fast and quiet.”
Swiss firm Camion Transport enthusiastic about electric vehicles
With a healthy dose of Swiss common sense, Camion Transport has been working for many years on achieving genuine sustainability in transport and since the spring of 2022 a DAF CF Electric has been playing an important role in the company’s eco-strategy. Three more DAFs will be added to the fleet.
By Stephan Manfredi
Camion Transport has a sizeable number of branches in Switzerland, but the company’s HQ is located in the town of Wil, halfway between Zurich and Lake Constance. This traditional Swiss firm has long been a trendsetter when it comes to the environment and social responsibilities. Back in 2010 Camion launched its sustainability programme Eco Balance by Camion Transport with the aim of enabling the company to take effective, future-proof and responsible steps. Their sustainability programme is underpinned by an important guiding principle: “Achieving a high level of economic performance with as little ecological impact as possible.”
Zero emissions
The ultimate goal of the entire operation is zero emissions by 2050 and the steps being taken to achieve that goal are ambitious. For example, they include the buildings, the generation of energy (solar) and the forklifts at the various locations. With regard to its vehicles, Camion Transport aims to be operating emission-free deliveries in city centres by 2025. The same will apply in greater urban areas by 2030 and by 2040 over half of its trucks and ‘last mile’ vehicles will also have zero emissions.
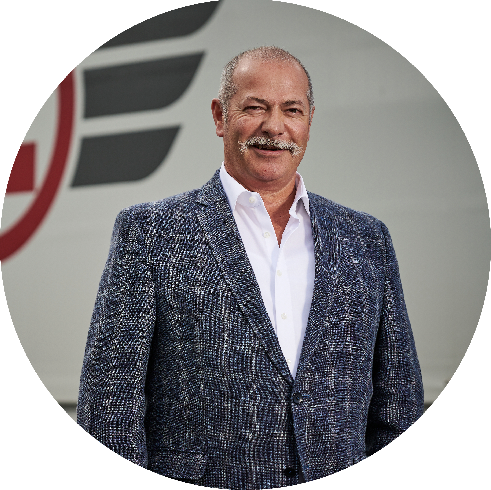
“As a company, we need to focus on what we can do today.”
Josef Jäger,
Chairman of the board of directors and Managing Director at Camion Transport
Railway
Established in 1925, Camion Transport has a long tradition in sustainability. “Our focus lies on the things we can do ourselves,” says Josef Jäger, chairman of the board of directors and managing director at Camion Transport. “As a company, we need to focus on what we can do today.” In other words, to be active in the areas where you can exercise direct control. “We look further than just the trucks themselves.” Camion Transport’s ambitions were already clear back in 1984 when it started using rail transport to move cargo between the head office in Wil and Geneva over a distance of 340 kilometres. That was the first step in establishing the rail shuttle network throughout Switzerland that connects the company’s fifteen different branches with each other today.
Innovation fleet
The fleet of more than six thousand vehicles is the beating heart of the firm. Like all other major transport companies, Camion Transport faces the question as to which driveline technology they should invest in to achieve zero emissions in an economical manner in the future. With this in mind, Josef Jäger and his team set up their innovation fleet in 2021. It contains twenty different emission-free vehicles that can be used to test alternative drivelines for different applications. Their goal is to have a purchasing strategy in place by 2024, not only for the trucks but also for the new infrastructure and ICT that will be required.
A first for Switzerland
The DAF e-truck was a first for Switzerland. “DAF was the first manufacturer that was able to supply a tractor in the desired configuration,” says Jäger, explaining their decision to choose DAF. The CF, with a peak power of 240 kW and a battery capacity of 315 kWh, operates from Vufflens-la-Ville near Lausanne, covering a distance of 200 kilometres each day. With a stop for recharging, this can even be extended to 300 kilometres. The experience gained has proved very valuable, confirms Jäger. The staff assigned to the vehicle had no trouble adapting and the drivers were soon impressed by the extremely quiet and comfortable driving experience.
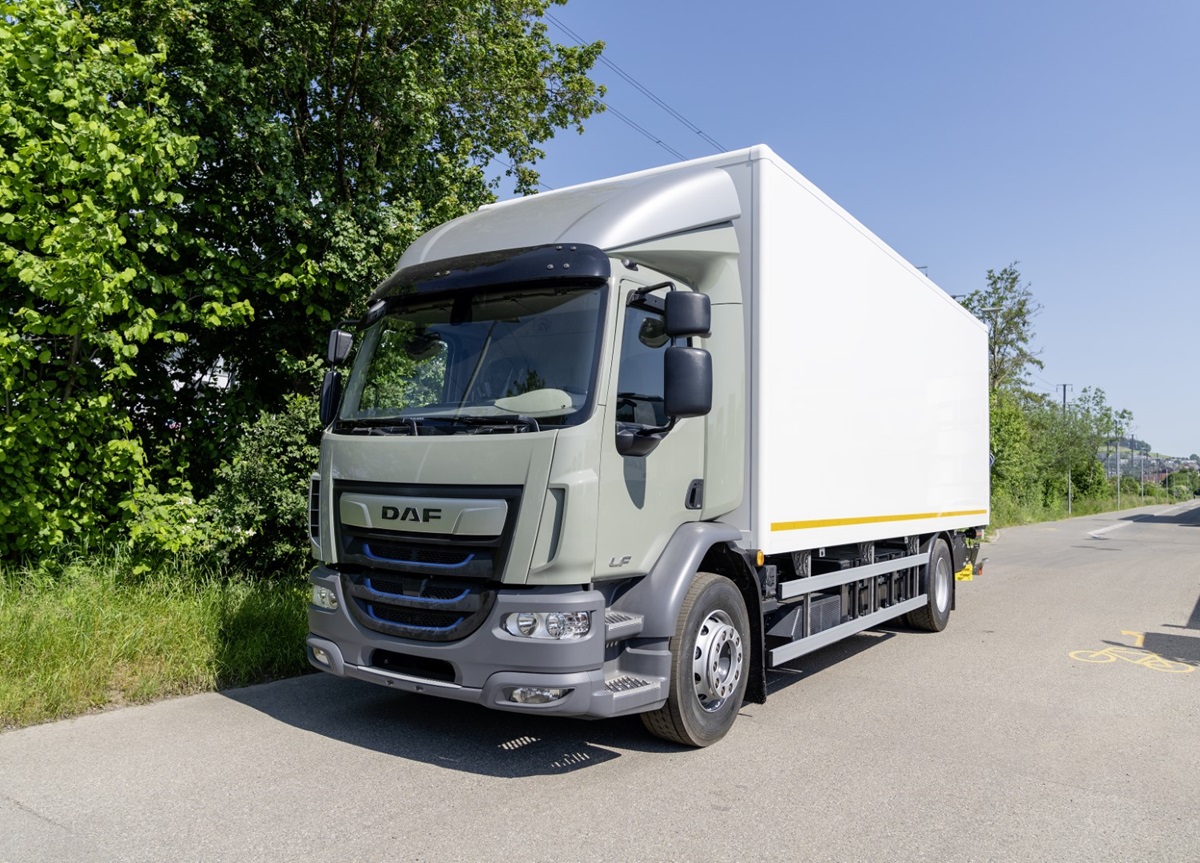
The LF Electric will transport goods in the Bellinzona-Lugano region from Camion Transport’s new Tessiner location.
CF and XD Electric
It is no coincidence that Camion Transport will be adding three electric DAFs to its fleet. Two of these will be XD Electrics. Camion Transport decided not to choose the most powerful version of the XD. However, the truck they did choose, with a battery capacity of 420 kWh and an engine capacity of 310 kW, will be more powerful and have a greater range than the CF. The CF and XD tractors will be used in the Lausanne region and in the east of Switzerland. The third truck is an LF chassis with a rigid body that belongs to the 18-tonne class. This LF Electric, with an engine capacity of 259 kW and a battery capacity of 254 kWh, will transport goods in the Bellinzona-Lugano region from Camion Transport’s new Tessiner location.
Support
The company is very happy with the support offered by the Swiss DAF organization. According to Josef Jäger, the professional support provided was extremely thorough, particularly because Camion Transport’s first CF Electric was also the first electric DAF to operate in Switzerland. From configuration to homologation to start-up, the level of technical support was outstanding, says Jäger. And this support was not confined only to the vehicles, as DAF also provided valuable input regarding the company’s needs in terms of charging infrastructure.
Road map
The three new DAF Electrics and other e-trucks are helping Camion Transport to plot a road map towards a sustainable future. Camion Transport is carefully monitoring the development of technologies such as e-fuels, biofuels and hydrogen, as well as the possibility of retrofitting electric drivelines in existing diesel trucks because they will probably have an impact on the company’s strategy in the future. “In my thirty years at Camion Transport, the pace of change has never been as fast as it is now,” says Josef Jäger. “That brings lots of challenges but also plenty of opportunities.”
New generation DAF XB urban distribution trucks
It has taken DAF less than two years to completely revamp its portfolio. Following on from the XF/XG/XG+ and the XD, the first information has been released regarding the New Generation XB, which will go into production at the end of the year. With the XB, DAF is launching a new series of high-quality urban distribution trucks that will also be available with a fully electric driveline.
With the New Generation XB, DAF is introducing a series of distribution trucks that is ready for a sustainable future. Available with both electric drivelines and clean diesel engines, the new XB-models will help transport companies to take another step towards zero emissions. The XB offers tailormade solutions in the 7.5 to 19-tonne class and is expected to set a new standard in urban and regional distribution. The vehicles are available in no less than three fully electric versions, respectively 12, 16 and 19 tonnes, that will make emission-free urban distribution a reality. These e-trucks also feature smart loading systems, both for on the road and back at base.
Comfortable, safe sustainable
DAF surprised the trucking world last year with its new XF/XG/XG+ series which raised the bar with regard to efficiency, emissions, driver comfort (so much space!) and safety. The XF/XG/XG+ was instantly voted ‘Truck of the Year 2022’. One year later the new XD saw DAF walk away once again with the prestigious ‘Truck of the Year’ award. And now, with the New Generation XB, a series that also includes the XBC construction truck, the distribution segment can benefit from vehicles that offer comfort and safety in combination with sustainable technology.
Plenty of power
The trucks’ sustainability is underlined particularly by the electric versions of the XB, which will make zero emissions possible for urban and regional distribution. There is an extremely user-friendly 12-tonne version available with 17.5-inch wheels and only one mounting step, in addition to the heavier 16 and 19-tonne versions. The wheelbases vary from 4.2 to 6.9 metres, illustrating the enormous range of superstructure possibilities. The XB’s electric motor is available with 120 or 190 kW nominal engine capacity and torques of 950 and 1,850 Nm respectively. The peak capacities of the electric motors are even more astounding: 2,600 and 3,500 Nm. The battery packs are environment-friendly in composition – they contain neither cobalt nor magnesium – and can be supplied with powers ranging from 141 to 282 kWh. This guarantees a range of over 280 kilometres, which has proven to be more than sufficient for urban distribution.
Loading solutions
A novel feature is the Combined Charging System on the DAF XB Electric that allows the vehicle to be charged using the normal electricity grid. This is ideal for the majority of distribution trucks, as they usually return at the end of the day to their home base where they can be recharged overnight. Of course, rapid charging is also possible using a 650v 150 kW DC charger and the truck can be charged from 20 to 80 per cent in around an hour. Charging times vary from 40 to 70 minutes, depending on the specifications. DAF has no shortage of experience with e-trucks and can support customers in the transition to electric. Such as advice on route planning, charging en route, driver training and choosing the most efficient PACCAR charging stations.
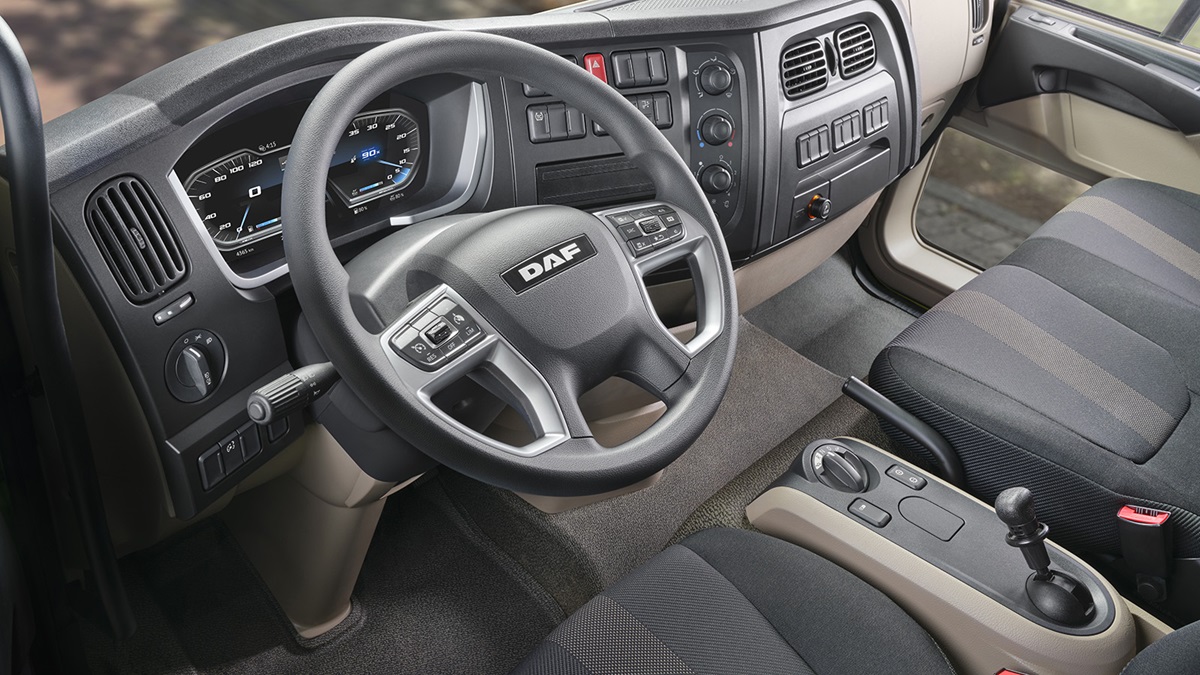
Comfortable chairs, a newly designed steering wheel and a large (12-inch) digital display make life on board even more appealing
Pick of the bunch
In addition to the e-driveline, there is also a wide range of modern PACCAR diesel engines available for the XB. These have been designed to deliver extra torque at low revs, making them very fuel efficient. Customers can choose between a 4.5-litre four-cylinder (PACCAR PX-5) and a 6.7-litre six-cylinder (PACCAR PX-7) engine with capacities ranging from 124 kW/170 hp to 227 kW/310 hp. Both engines are suitable for the use of HVO, which can reduce CO2 emissions by up to 90 per cent. For the transmission there are manual six- and nine-gear gearboxes available, as well as fully automatic Allison transmissions for special applications. The pick of the bunch, however, is the fully automatic Powerline transmission with eight gear steps. It enables smooth gear shifting, which in turn guarantees pulling power, maximum comfort and ease of driving. Drivers will also appreciate the fact that the truck begins to move itself upon release of the brake pedal. This makes manoeuvring a lot easier.
Workplace
As with the XF/XG and XD series, when designing the XB DAF paid a lot of attention to the space in which the men and women driving the truck do their work. The XB is available with day cabs (with optional extension) and sleeper cabs, both of which are positioned low and fitted with smart steps for optimal access. Comfortable chairs, a newly designed steering wheel and a large (12-inch) digital display make living and working in the DAF XB even more appealing. The display shows all relevant vehicle information at a single glance and the settings can be adjusted to suit each individual driver.
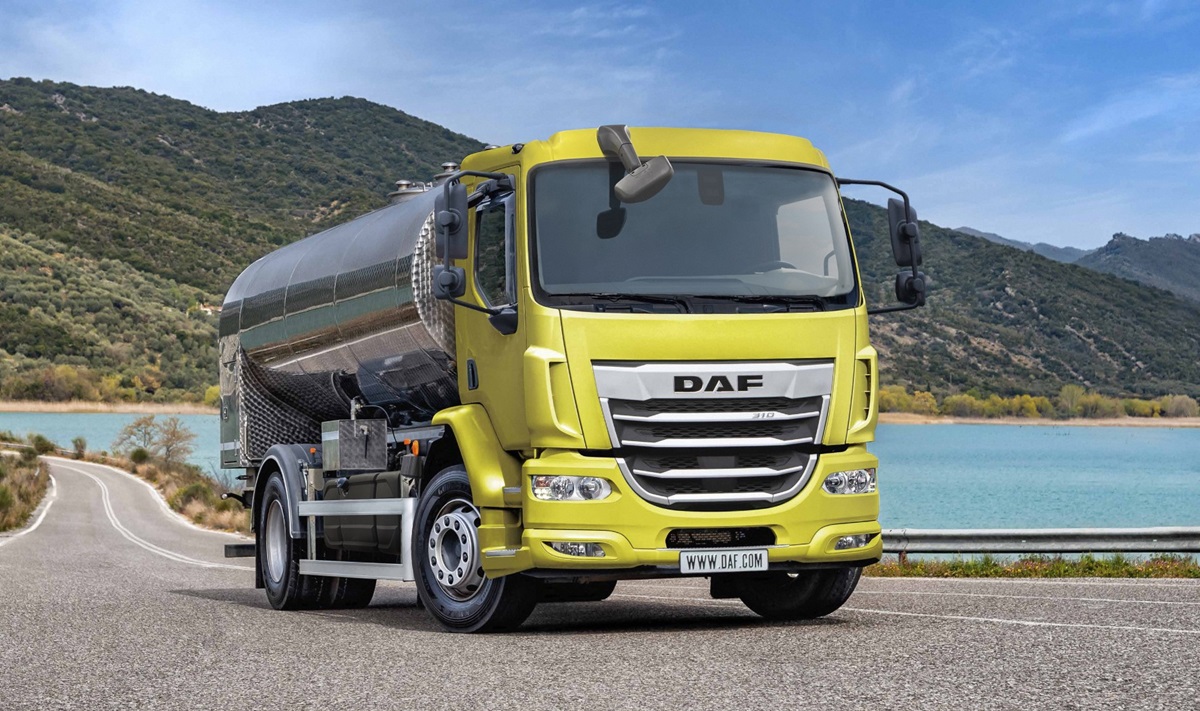
With the New Generation XB, DAF is introducing a series of distribution trucks that is ready for a sustainable future. As with the XF and XD, the chassis on the XB is fitted with a cleverly designed grid pattern, making it extremely superstructure-friendly
Superstructure-friendly
Vehicle efficiency is also an important factor and the DAF XB certainly does not disappoint. The smallest wheelbase is 4.2 metres, while the largest is almost three metres bigger: 6.9 metres. This allows for superstructures of up to nine metres in length. The net weights have been kept low, which facilitates high loading capacities. As with the XF and XD, the chassis on the XB is fitted with a cleverly designed grid pattern, making it extremely superstructure-friendly. A new feature is the predefined chassis lay-out specifically designed for street sweepers and tippers. The exhaust systems, batteries and air tanks are located in the ideal positions, which saves the customer both time and money.
Construction truck
DAF has developed an XBC series especially for the construction segment that can work both on and off the road, in addition to a full series of XD and XF construction vehicles. The XBC trucks have a 19-tonne chassis and a ground clearance of over 25 centimetres. An approach angle of 25 degrees, a steel radiator plate that protects the engine compartment and an extra robust front bumper in lava grey are clear evidence that this truck can easily hold its own in any environment.
Value
These qualities apply across the board to the entire DAF XB series, which will go into production at the end of the year and is set to prove its value to the distribution segment. With its sustainable transport solutions for both the electric and fueldriven versions, excellent driver comfort and incredible range of superstructure possibilities, the XB is a DAF masterpiece in every sense of the word.
Ewout van Wijk sees the future in e-trucks
The Dutch E. van Wijk Group ordered no less than ten DAF XD Electrics. For CEO Ewout van Wijk, it is crystal clear that battery-electric vehicles are the future. We met up with this dynamic entrepreneur for a conversation about sustainable transport. “I’d love to have those ten e-trucks out on the road tomorrow.”
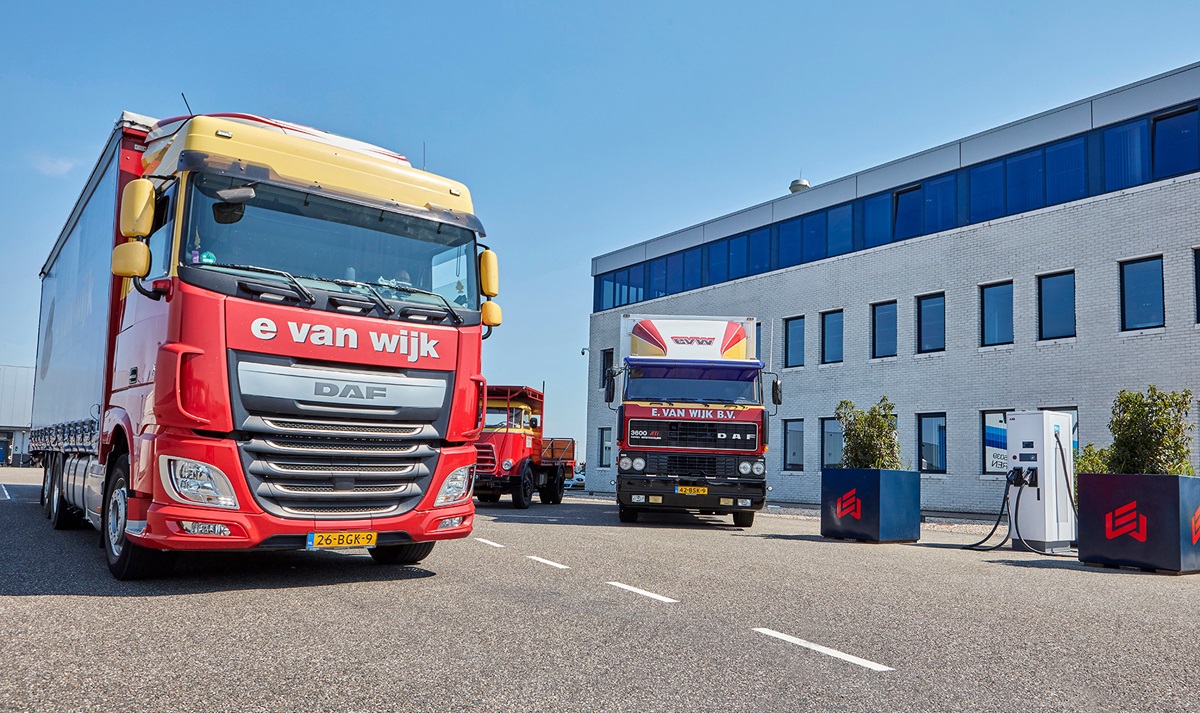
“We have been using diesel for 75 years but we have to make the switch to something else”
Knowledge
Ewout van Wijk belongs to the third generation of van Wijks to run the family business, which is celebrating its 75th anniversary this year. His grandfather, Ewout (the ‘E’ in the company name) started the business in 1948 before handing the reins over to his father, Ad, who in turn handed them to Ewout (37) four years ago. The company currently employs eight hundred people at two locations in the Netherlands, two in Romania and one each in Poland and Ukraine. Ewout has taken on the role of CEO at a very interesting time. The new boss has taken up the challenge, one in which he intends to apply his thorough knowledge of electric alternatives. “I might be the Chief Executive Officer of Van Wijk, but over the next few years I’m more likely to be the Chief Energy Officer,” he says with a smile.
Alternative
The smile is soon replaced by a more serious look when he explains how the transport world needs to understand that road transport needs an alternative for fossil fuels. “Just look at the new regulations, like the Heavy Goods Vehicle Charge Act that will come into force in 2026. Europe is already implementing far-reaching measures by increasing the duties on diesel so that it can fund the energy transition, while here in the Netherlands they are going even further. When I realised the implications I knew that if we don’t start doing tests now, we are going to fall behind. We have been using diesel for 75 years but we know we have to make the switch to something else. It will start with battery-electric trucks but I still don’t know what will come after that. I’m not saying hydrogen technology is not going to work, but it certainly is not going to happen in the short term.”
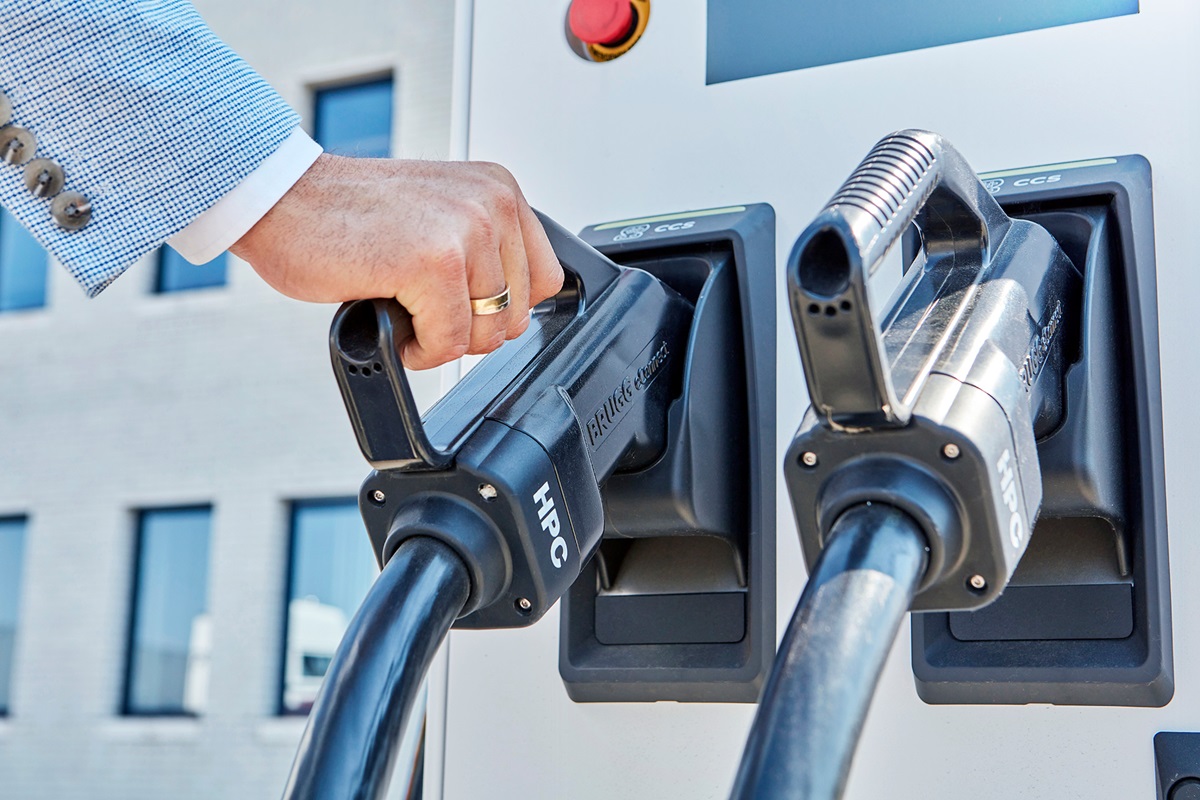
A DC charger has been installed at the company’s premises in Giessen in anticipation of the first electric DAF test vehicle
CO2-emissions
And that’s why Van Wijk has ordered ten new e-trucks from DAF. They have already installed a DC charger at the company’s premises in Giessen and Ewout has immersed himself in the world of kilowatts, charging stations and green energy. “At first I didn’t even know the difference between a kilowatt (kW) and kilowatt hour (kWh). But it didn’t take long for me to realise that if I wanted to have electric trucks in the future, I would have to do something about our electricity grid connection. A lot of other companies discovered the same, too. In our strategy, we laid out our plans to reduce our CO2 emissions by a quarter in 2025 compared with 2020. We have already taken various steps and the company has a history of investing in new equipment, even in small things like LED lighting. We have made our building more sustainable, but we have to be face the fact that our trucks are the greatest source of CO2 emissions.”
Kilowatt hours
Van Wijk knew that he would have to dive deeper into the world of electric trucks. “There were plenty of stories about electric vehicles: too many obstacles, the government needs to subsidise it, the customer has to foot the bill, etc. But I want to know how it all works before I go to the customer or the government. My first question was, will I need a different grid connection? And if so, what will that cost? In any case, our current connection doesn’t provide enough kilowatts, that’s for sure. And there’s a surplus of electricity on the grid too, so I can’t even sell it back. In the end I decided to apply for the most powerful connection available – 6 MVA – and we’re currently on the waiting list. In the meantime, we’re going to have to come up with creative solutions ourselves. We’ve covered the roof with solar panels and bought a 4,300 kWh battery, so with the battery, solar panels and our current grid connection we should be able to power ten e-trucks for the next two or three years.”
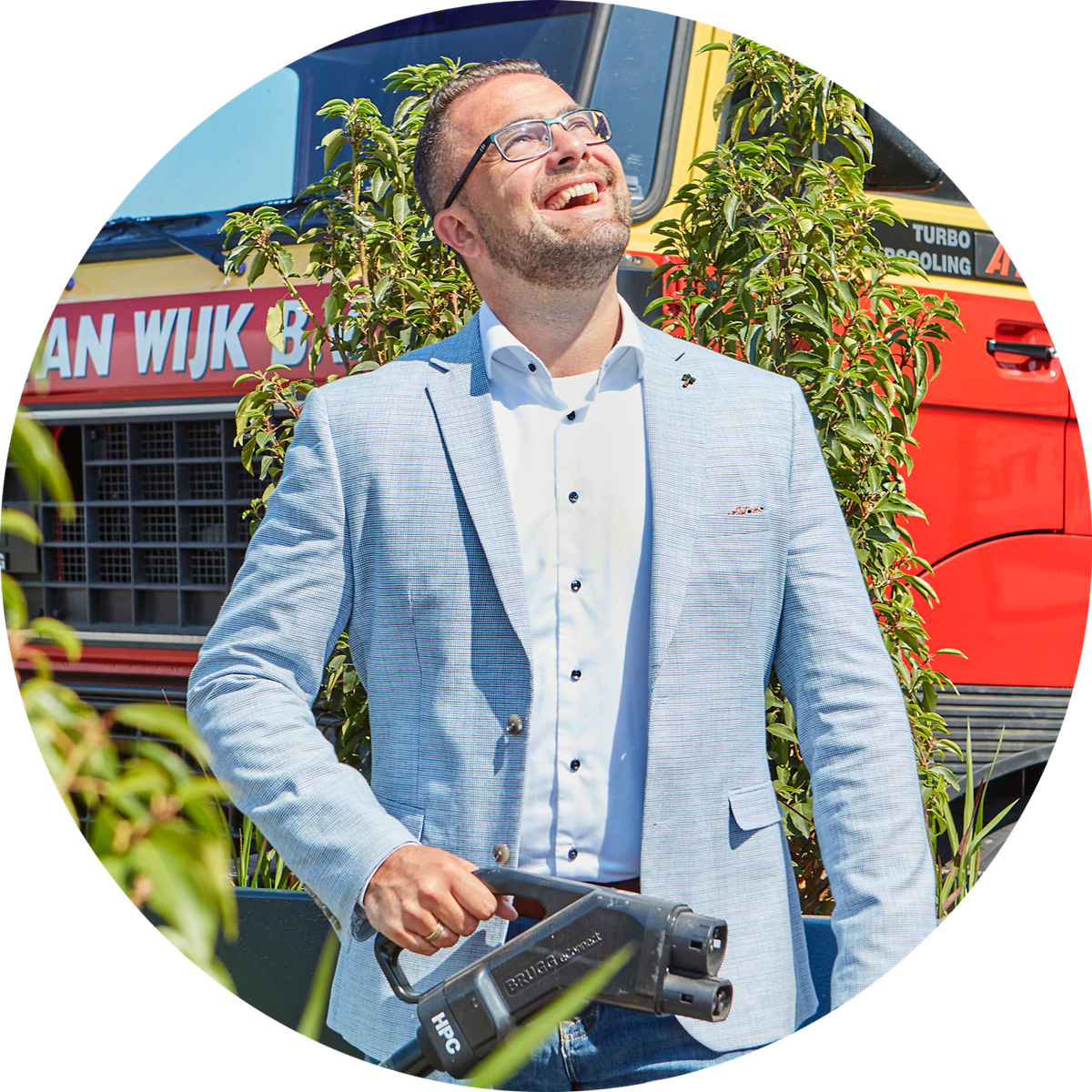
“We capture the sun’s energy here and use it to power our trucks. And the government even pays us to do so”
Ewout van Wijk,
CEO E. van Wijk Group
Network operator
Van Wijk also found out that it is useful to talk to your network operator. “I would advise everyone to do this. Find out not only what’s possible but also how to tackle the ‘impossible’ stuff,” says Van Wijk, who believes it is all less complicated than you might think if you are prepared to do some digging. “I often say to people: imagine you’re at a filling station and all of a sudden it starts raining diesel. What would you do? You’d probably go and find as many buckets as you can carry. We don’t expect it to start raining diesel, of course, but what about all that sun? We capture the sun’s energy here and use it to power our trucks. And the government even pays us to do so because they believe we’re on the right track.”
Busy with energy
Being busy with energy is going to be very important for transport companies, says Ewout van Wijk. “Every transporter knows the price of diesel every single day. But if you ask them ‘What does a kilowatt hour cost today?’ they haven’t a clue. Which is not very handy because it changes every hour. Yesterday, the grid was even paying you for your kilowatt hours! The system actually allows me to trade in electricity, just like in the horticulture sector. A network operator recently rang me and asked, ‘How big is that battery of yours?’ I said, ‘4,300 kilowatt hours’. They were immediately interested. So you see that network operators are having to change, too. If you’re a transporter and are about to acquire a large fleet of e-trucks, there’s no getting around the fact that you are going to be very busy with energy in the coming years.”
Seesaw
Putting ten electric DAFs into operation is set to be a serious project and one with an eye on the future, according to Van Wijk. “We will look at things like where they can be used and how they will work in practice. I see it as a business case that we can build around those ten e-trucks. Of course, I’d like to be able to have them on the road tomorrow instead of later. It’s also important to consider the economics of acquiring an e-truck. What a lot of other companies don’t know is that the government is going to employ a seesaw policy over the next few years. This means they are going to tax the industry more heavily – including diesel trucks, but what I think of that right now is not relevant – and use the funds to invest in the energy transition. This will include subsidies and a trading system for CO2 emission rights. If you plan carefully, you can get the TCO (Total Costs of Ownership) of an e-truck down below that of a diesel truck within a very short period”, says Van Wijk. “That’s probably the best kept secret in the Netherlands at the moment.”
Focusing on sustainability: a shared responsibility
Someone once said we have not inherited the Earth from our ancestors but are borrowing it from our children. We all need to share the responsibility for caring for our beautiful planet so that we can pass it on in good health to our children and future generations.
When we zoom in on the transport sector we can see that all parties, including truck manufacturers and transport companies, are doing their utmost to reduce CO2 emissions and lessen their effect on the environment. The same also applies to the air quality in our cities.
DAF and its parent company PACCAR are busy developing new solutions for clean and sustainable road transport. However, there is no one-size-fits-all solution for all transport applications and that is why we are exploring several different avenues: from fully electric to hybrid and from hydrogen in combustion engines to hydrogen in a fuel cell. Existing combustion engines must also be taken into consideration, as they will continue to be the most sustainable and efficient option for long distance transport in the years to come, especially when powered by HVO or, in the more distant future, new generations of fuel.
Our customers are also busy exploring more sustainable and future-proof solutions for their business operations. Naturally, we are helping them in every way we can because we share a common goal. In this edition of DAF in Action you can read about our customers’ experiences and their vision of the future of sustainable road transport.
We must not forget the role that governments have to play in the drive towards sustainability. The EU has set the transport industry extremely challenging goals but both we and our customers expect something in return for our efforts. It is the responsibility of governments to ensure that they invest in and stimulate the required infrastructure so that the first zero-emission trucks can hit the road.
We are living in challenging times. But if everyone puts their shoulder to the wheel, I see a bright future ahead for us all.
Harald Seidel
President
DAF Trucks N.V.